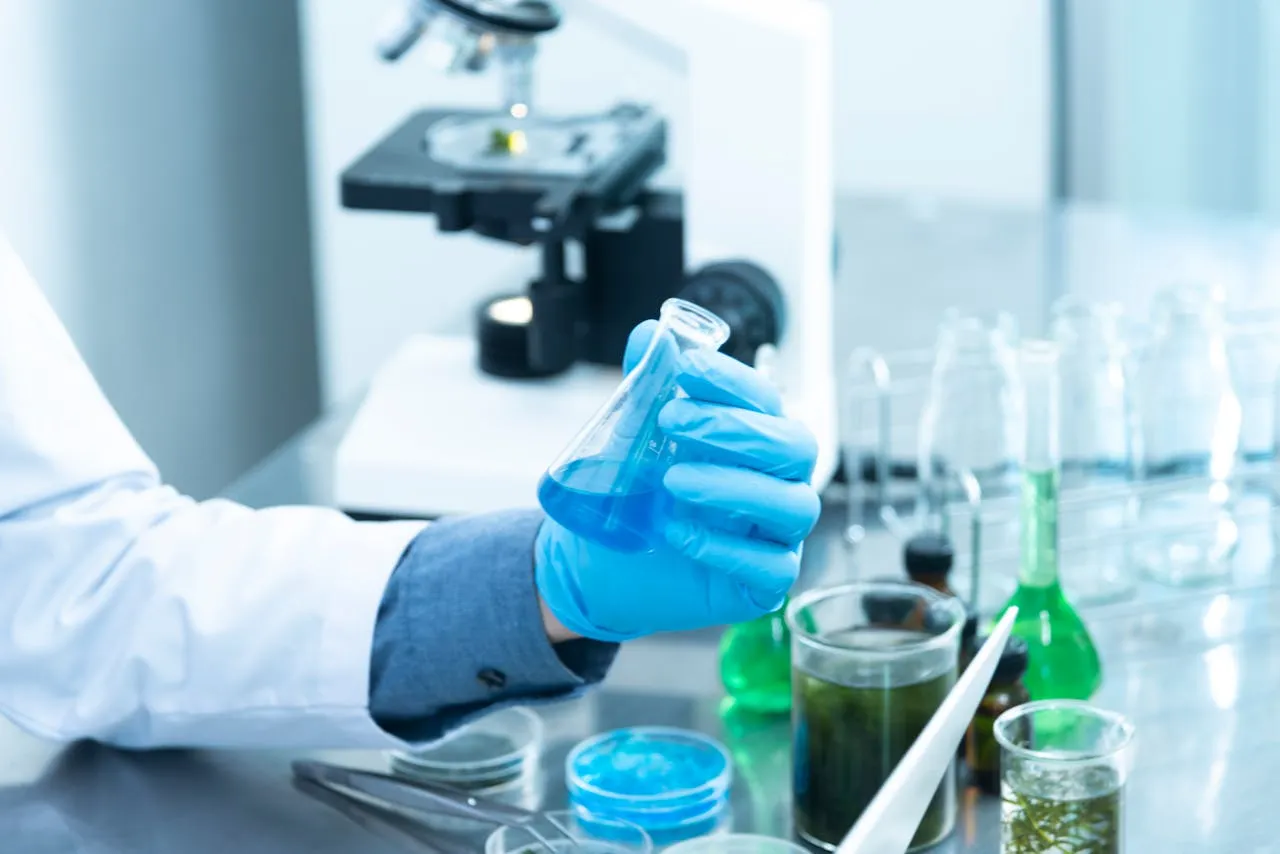
Shin-Etsu Chemical Co., Ltd. (TOKYO: 4063) has introduced advanced equipment for manufacturing semiconductor package substrates using a novel method. This equipment employs a high-performance excimer laser system, applying the dual damascene method from the semiconductor front-end process to the package substrate back-end process (known as the Shin-Etsu dual damascene method). This innovation integrates interposer functions directly into the package substrate, eliminating the need for a separate interposer and enabling finer microfabrication not achievable with traditional methods. Additionally, it reduces costs and capital investment by eliminating the photoresist process typically used in package substrate manufacturing.
The technology supports chiplet integration, where individual circuits are assembled and connected within a package to reduce manufacturing costs for high-performance semiconductors. By eliminating the interposer, the assembly process is simplified significantly. The method involves connecting chiplets directly to the package substrate using wiring patterns that replicate interposer functions, thereby shortening assembly times and reducing costs associated with advanced semiconductor manufacturing.
The equipment utilizes sophisticated microfabrication techniques to directly form intricate electric circuit patterns within multiple organic insulation layers of the package substrate, followed by copper plating for circuit formation. It employs an excimer laser as a light source to batch-process large-area electric circuit patterns efficiently. The Shin-Etsu dual damascene method enables further miniaturization beyond what is achievable with the current semi-additive processing (SAP) method using dry film resist.
Shin-Etsu Chemical’s laser processing equipment can handle areas of 100 mm square or larger, utilizing specially designed photomasks and lenses to achieve precise results. Processing times vary depending on substrate size but are consistent for forming wiring patterns, electrode pads, and vias. For instance, it takes approximately 20 minutes to create trenches and electrode pads on a 515 mm × 510 mm organic substrate, alongside forming vias of specified dimensions.
The company is actively integrating its material and equipment technologies to offer comprehensive solutions in semiconductor manufacturing. By pioneering new process technologies, Shin-Etsu Chemical aims to lead advancements in next-generation technologies, contributing to the development of a prosperous society.