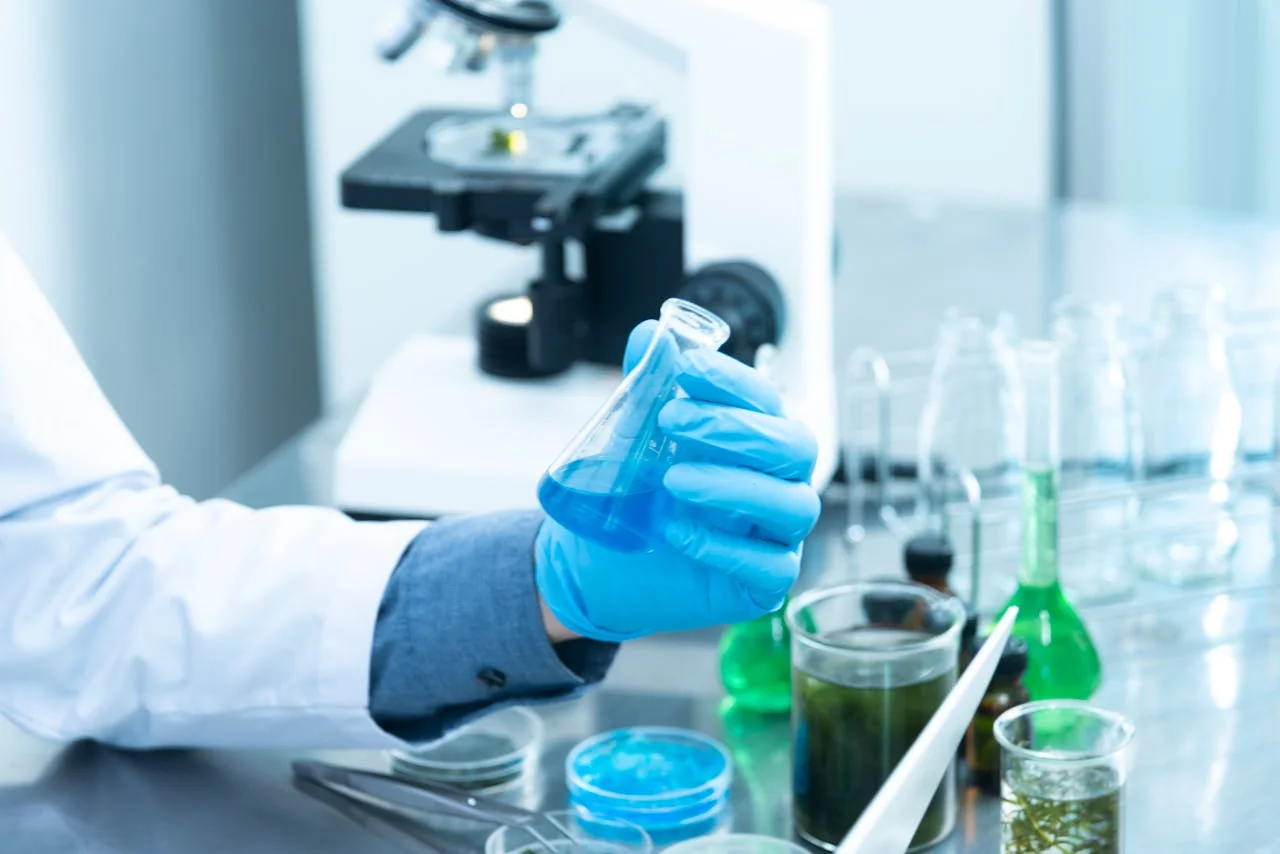
Shin-Etsu Chemical Co., Ltd. has introduced advanced equipment for manufacturing semiconductor package substrates using a novel approach, following their previous success with micro-LED systems. This new equipment employs a high-performance process utilizing excimer lasers, applying the dual damascene method typically used in the front-end semiconductor manufacturing to the package substrate production process (known as the Shin-Etsu dual damascene method). This innovation integrates the functions of an interposer directly into the package substrate, eliminating the need for a separate interposer and enabling unprecedented levels of microfabrication that traditional methods couldn’t achieve. Notably, this advancement reduces costs and capital investments by eliminating the photoresist process in package substrate manufacturing.
The industry has shown interest in chiplets, which are individual circuits that are assembled into a single package to reduce the manufacturing costs of high-performance semiconductors. This technology necessitates mounting multiple chiplets on an intermediate substrate called an interposer and connecting them. However, with Shin-Etsu’s dual damascene method, the interposer becomes unnecessary, streamlining the assembly process. Chiplets are now connected directly to the package substrate using wiring patterns that provide equivalent functionality to an interposer. As a result, the assembly process for advanced semiconductor devices employing chiplet technology is shortened significantly, leading to substantial cost reductions.
The newly developed equipment incorporates sophisticated microfabrication technology, allowing intricate electric circuit patterns to be directly formed within each organic insulation layer of a multi-layered package substrate, followed by circuit formation through copper plating. It utilizes an excimer laser as a light source to batch-process large-area electric circuit patterns. The Shin-Etsu dual damascene method enables further miniaturization and microfabrication that was previously unattainable with the current mainstream semi-additive processing (SAP) method using dry film resist. The laser processing equipment can handle areas of 100 mm square or larger in a single operation using Shin-Etsu’s large photomask blanks and unique special lens. The processing time is consistent regardless of the number of vias, with trenches, electrode pads, and vias processed simultaneously. For instance, on a 515 mm × 510 mm organic substrate, the equipment takes approximately 20 minutes to create trenches and electrode pads of specific dimensions.
Shin-Etsu Chemical is actively integrating its material and equipment technologies to develop new process technologies. By offering comprehensive solutions encompassing both equipment and materials, the company aims to lead the development of next-generation technologies and contribute to the creation of a prosperous society.