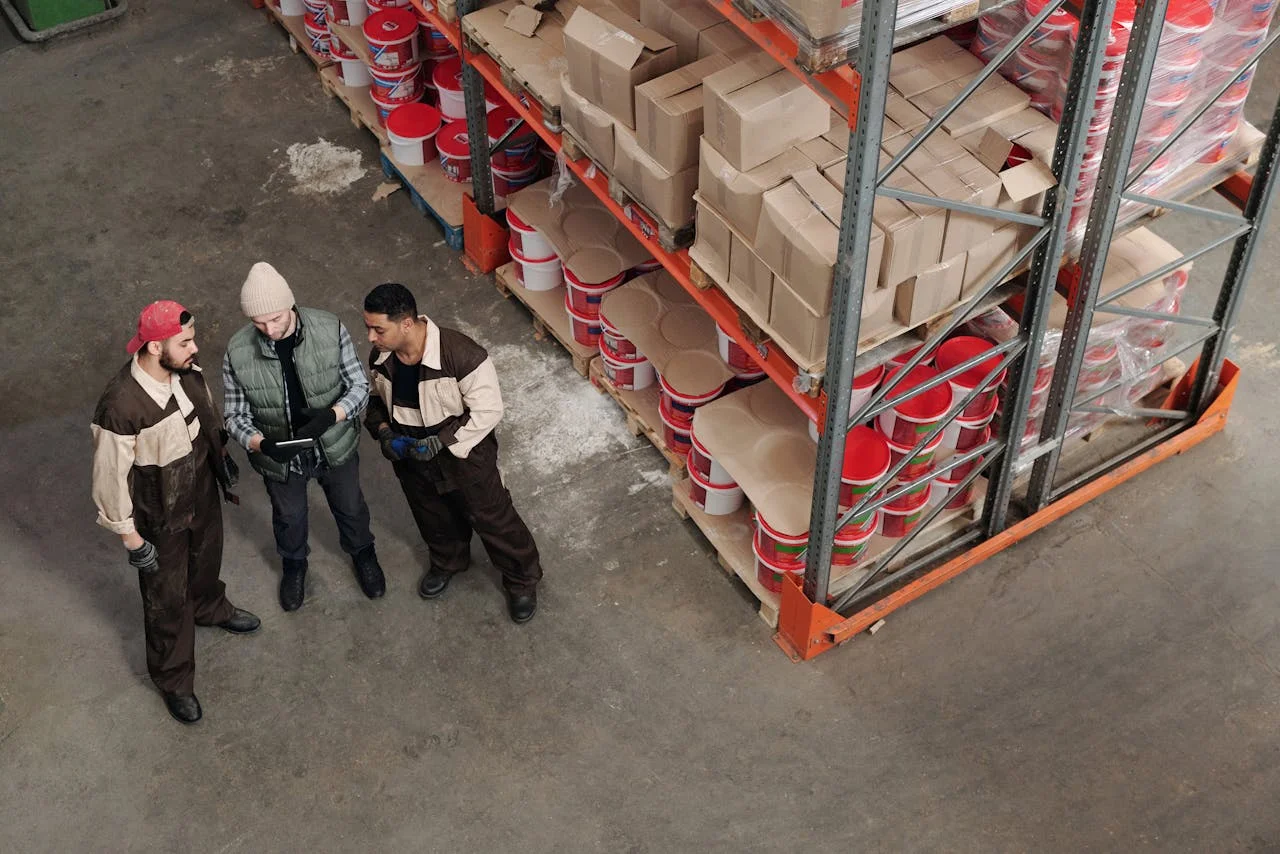
SABIC, a global chemical industry leader, has partnered with Lamb Weston, a major producer of frozen potato products, and Opackgroup’s Oerlemans Plastics to create sustainable, low-weight packaging made from bio-renewable materials. The packaging uses a thin coextrusion film structure, with at least 60% of the material derived from bio-feedstock made from used cooking oil (UCO). This UCO is collected from Lamb Weston’s production, converted into certified bio-renewable high-density polyethylene (HDPE) and metallocene linear low-density polyethylene (mLLDPE) polymers, and then transformed into multilayer PE film for pre-fried frozen potato products.
Khaled Al-Jalawi, SABIC’s Global Director of Circular Economy Business, emphasized the project’s circular approach, which utilizes UCO to produce recyclable polymers. The packaging, certified under the International Sustainability & Carbon Certification (ISCC) PLUS regime, has at least 60% renewable content from the polymers to the final film.
Sebastiaan Besems, VP Commercial EMEA at Lamb Weston, noted the shift in consumer and retailer preferences towards sustainable packaging. The new packaging aligns with the brand’s sustainability goals, reducing the carbon footprint by 30% and cutting packaging weight by 20%. It supports Lamb Weston’s broader plans to halve food waste, reduce the overall product carbon footprint by 25%, and achieve more circular production by 2030.
Laura Hanegraaf, Sales Manager at Oerlemans Plastics, highlighted the project’s commitment to promoting low-carbon, renewable products in the flexible film industry.
The packaging solution not only ensures a 30% lower carbon footprint compared to previous versions but also meets the food safety requirements of both the European Food Safety Authority (EFSA) and the U.S. Food and Drug Administration (FDA). The SABIC HDPE resin provides high strength and flexibility, while the SUPEER mLLDPE resin ensures excellent bag sealing.