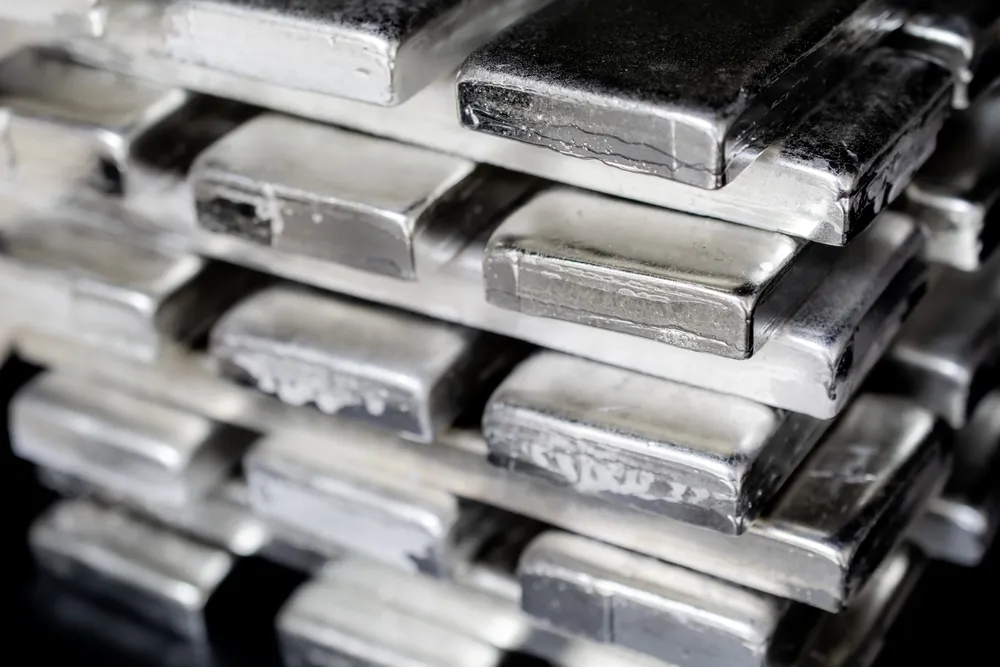
Pure Lithium Partners with Kingston Process Metallurgy to Advance Scalable Lithium Metal Anode Production for Next-Generation Battery Technology
Boston, MA – Pure Lithium Corporation, a Boston-based leader in advanced battery materials and vertically integrated lithium metal battery technology, has announced a significant strategic collaboration with Kingston Process Metallurgy Inc. (KPM). This partnership marks a pivotal milestone in Pure Lithium’s mission to revolutionize lithium battery technology by scaling the production of lithium metal anodes using a novel, sustainable, and cost-effective method.
The agreement brings together Pure Lithium’s innovative Brine to Battery™ electroplating process and KPM’s extensive experience in metallurgical engineering and process scale-up. Together, the companies will co-design, construct, and commission a pilot-scale lithium metal anode production reactor, with the ultimate goal of accelerating commercialization of lithium metal batteries that are safer, more energy-dense, and more affordable than current lithium-ion technology.
Pioneering a New Era of Lithium Metal Batteries
Pure Lithium’s proprietary Brine to Battery™ approach fundamentally disrupts traditional lithium production by skipping intermediate steps like lithium carbonate or lithium hydroxide conversion. Instead, the company directly electroplates high-purity lithium metal from lithium-rich brine sources onto anode substrates, eliminating both cost and environmental inefficiencies in the conventional lithium supply chain.
Unlike conventional lithium-ion batteries that rely on graphite anodes, Pure Lithium’s advanced battery platform uses lithium metal anodes paired with vanadium oxide cathodes, resulting in superior energy density, longer cycle life, and enhanced performance across a wide range of temperatures. The technology has the potential to leapfrog current generation batteries, unlocking the full capabilities required for electric vehicles (EVs), grid-scale storage, aerospace applications, and defense systems.
To make this vision a reality, Pure Lithium recognized the need to bridge the gap between laboratory-scale breakthroughs and industrial-scale manufacturing. That’s where Kingston Process Metallurgy comes in.
The Role of Kingston Process Metallurgy
Kingston Process Metallurgy (KPM), based in Kingston, Ontario, is renowned for its ability to develop, de-risk, and scale complex chemical and metallurgical processes from bench-scale experiments to commercial plants. With a multidisciplinary team of chemical engineers, metallurgists, and material scientists, KPM has become a trusted partner for technology-driven companies seeking to bring innovative concepts to life.
Under this new collaboration, KPM will lead the design and engineering of a fully integrated pilot-scale lithium metal reactor. This system will not only demonstrate the technical feasibility of Pure Lithium’s electroplating method but also optimize it for scalability, reliability, and cost efficiency.
Key objectives of the project include:
- Reactor Design Optimization: Tailoring a scalable, modular reactor system capable of operating under industrial conditions with high throughput and yield.
- Quality Control and Purity: Ensuring consistent production of lithium metal anodes with high purity and customizable thickness to meet the requirements of various battery formats.
- Integration of Materials Recycling: Embedding a closed-loop recycling system that reduces material waste and supports circular economy principles in battery manufacturing.
- Economic Viability Demonstration: Establishing a clear path to commercial production by showcasing the cost advantages and sustainability benefits of the Brine to Battery™ process.
Strategic Vision and Technical Milestones
Pure Lithium’s integrated approach is unlike anything currently available in the lithium battery landscape. By controlling every stage of the value chain—from raw brine sourcing and selective extraction to electrochemical plating and recycling—the company is positioned to offer a vertically integrated solution with unmatched efficiency and environmental stewardship.
The pilot-scale reactor is expected to serve as a testbed for process optimization, allowing Pure Lithium to refine its operating parameters, validate performance metrics, and generate production data that will inform the development of future commercial-scale plants. The ultimate goal is to deploy these systems at brine-rich sites around the world, enabling on-site lithium metal anode production and reducing dependence on long, carbon-intensive supply chains.
In the words of Emilie Bodoin, Founder and CEO of Pure Lithium:
“Our lithium metal anode technology was a necessary first step to commercializing our lithium metal batteries. Without this technology at scale, these batteries would never reach commercialization due to the high cost and low quality of lithium metal produced by existing methods. I was first introduced to Kingston Process Metallurgy during my time with Argonne National Laboratory, and I am pleased to work with them, given their deep expertise in metallurgical system design and development.”
She continues:
“The team at KPM will play a critical role in scaling our innovative lithium electroplating technology into a fully operational pilot-scale reactor. Their hands-on approach and experience in scaling complex processes gives us confidence as we move toward pilot-scale production and continue building a truly next-generation lithium metal battery at a commercially viable price point.”
Addressing Industry Challenges with Breakthrough Innovation
The current lithium battery supply chain is riddled with inefficiencies, geopolitical risks, and environmental concerns. Traditional lithium mining and refining methods require extensive chemical processing, high energy input, and generate significant waste. Furthermore, the lithium metal used in next-generation batteries is currently expensive and difficult to produce at scale, limiting its use in commercial applications.
Pure Lithium addresses these challenges head-on by offering a sustainable, localized alternative. Its electroplating process enables the direct conversion of lithium ions from brine into battery-grade lithium metal without the need for chemical reagents or large-scale refining infrastructure. The process is designed to be modular and deployable close to lithium resources, thus reducing transportation costs, carbon emissions, and geopolitical dependency.
By eliminating reliance on lithium carbonate or hydroxide as intermediates, Pure Lithium’s Brine to Battery™ method significantly reduces production costs—an essential step toward making lithium metal batteries economically competitive with conventional lithium-ion cells.
The Road Ahead: From Pilot Plant to Global Deployment
Following successful commissioning of the pilot reactor, Pure Lithium plans to launch its first commercial pilot facility in a brine-rich region, where it will deploy its electroplating system at a larger scale. This facility will serve both as a production site and a demonstration center for potential customers and partners across the battery manufacturing ecosystem.
The company’s long-term strategy involves licensing its Brine to Battery™ technology to brine producers, battery OEMs, and energy companies seeking to integrate low-cost lithium metal anode production into their operations. Additionally, Pure Lithium is exploring strategic partnerships in the energy storage and automotive sectors to co-develop battery packs tailored to specific applications.
A Strong Foundation of Expertise
Both Pure Lithium and KPM bring decades of expertise and innovation to the table. Pure Lithium’s team includes battery scientists, electrochemists, and engineers with deep knowledge in lithium chemistry and advanced battery systems. Its founder, Emilie Bodoin, is recognized for her work on lithium systems at Argonne National Laboratory and has built a company culture rooted in innovation and scientific rigor.
Kingston Process Metallurgy, meanwhile, has a strong track record of scaling up novel chemical and metallurgical technologies across sectors including battery materials, mining, rare earths, and specialty chemicals. Their custom pilot plants and reactor systems have helped launch several emerging technologies into commercial success.
Together, the two companies are uniquely equipped to accelerate the transition to a clean energy future by enabling the next generation of lithium metal batteries—batteries that are safer, lighter, longer-lasting, and more environmentally responsible.
Pure Lithium Corporation
Pure Lithium Corporation is a vertically integrated battery technology company based in Boston, MA. The company is pioneering the Brine to Battery™ process to produce high-purity lithium metal anodes directly from brine resources. Its innovative lithium metal battery platform combines advanced electroplating, selective lithium extraction, and vanadium oxide cathode chemistry to deliver superior performance for electric vehicles, grid storage, and other high-demand applications.
Kingston Process Metallurgy Inc.
Kingston Process Metallurgy (KPM) is a privately held Canadian engineering firm specializing in process development, scale-up, and custom reactor design for clients across the chemical, metallurgical, and materials science industries. With a strong focus on innovation, technical excellence, and collaboration, KPM supports companies from concept to commercialization.