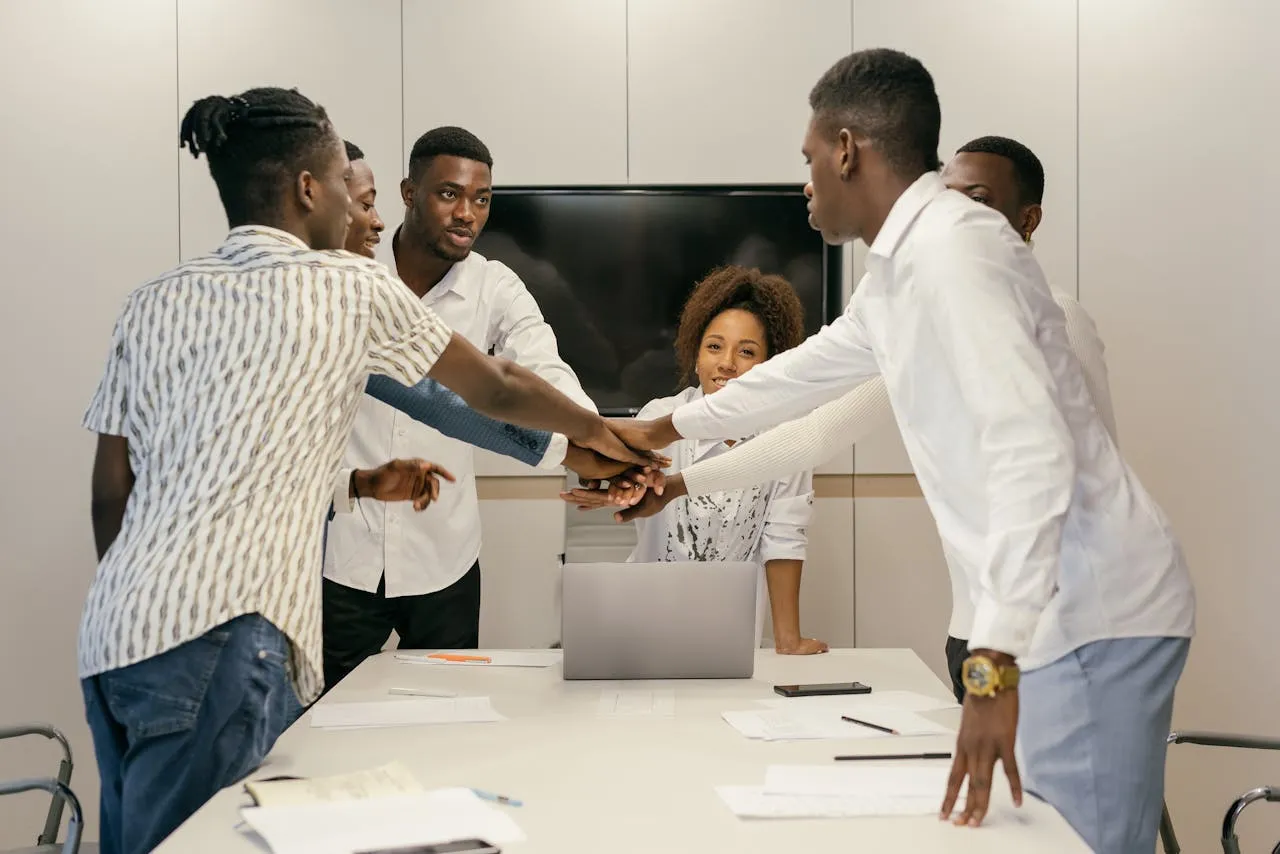
In collaboration with digital manufacturing leader Protolabs, NASA engineers recently demonstrated their AI-driven design tool at the PowerSource Global Summit, an annual conference uniting technology leaders across various fields. During the conference’s opening day, NASA engineers challenged participants to contribute inputs for generative design aimed at creating a prototype apparatus. This device would collect gas samples released when sunlight hits the moon, a part of NASA’s ongoing Artemis moon exploration missions.
The constraints provided by the crowd defined specific characteristics for the sample collection container, including modularity, stack-ability, scalability, and considerations for human or robotic interaction. Simultaneously, the geometries and part qualities had to ensure machinability while meeting strict size requirements.
Using NASA’s generative design software, a CAD file was generated based on these constraints, ready for machining at Protolabs’ digital factory the same evening. The objective was to produce the part before the conference concluded two days later.
“For this demonstration to succeed, it was critical that our manufacturing partner deliver the ordered part on-time without any margin for error or delay,” explained Matthew Vaerewyck, a mechanical engineer at NASA’s Goddard Space Flight Center in Greenbelt, Md. Protolabs was uniquely suited for this task, being the world’s only digital manufacturer combining a seamless digital thread with unmatched speed, reliability, and quality.
Vaerewyck uploaded the CAD file to Protolabs’ digital quoting platform. The organic design underwent 19 hours of toolpathing at Protolabs’ CNC machining facility in Minnesota. Subsequently, the part was shipped to the conference in Florida, arriving before the final day’s events, less than 36 hours after the initial order placement.
This pioneering experiment was hailed as a resounding success. NASA effectively showcased the benefits of generative design in reducing iteration cycles and significantly cutting down development time, while ensuring the creation of parts meeting rigorous spaceflight requirements. Protolabs, leveraging its rapid-turnaround digital manufacturing capabilities, played a pivotal role in bringing the prototype to life for conference attendees to witness.
“We are thrilled to have served as the manufacturing partner in this groundbreaking initiative, highlighting the transformative potential of combining generative design with automated manufacturing,” remarked Greg Thompson, senior director of CNC machining at Protolabs. “As a company at the forefront of manufacturing innovation, Protolabs takes pride in contributing to NASA’s mission to advance the frontiers of space exploration.