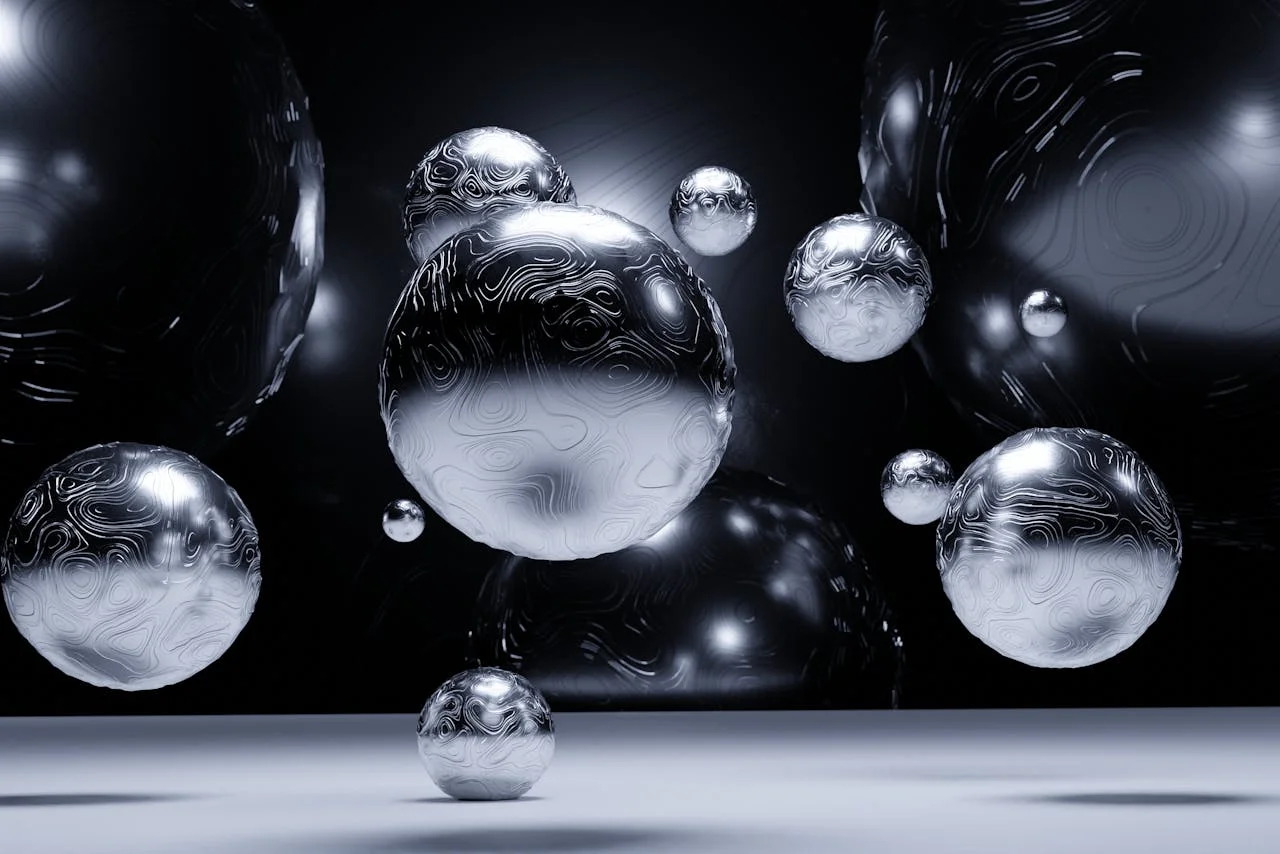
Mantle, a leader in metal 3D printing technology for precision tooling, announced today that it has secured $20 million in Series C funding. This milestone raises the company’s total funding to over $61.5 million and represents a significant step towards the widespread adoption of its advanced precision metal manufacturing technology.
The Series C funding round is set to significantly bolster Mantle’s rapid market expansion, scale up manufacturing capabilities to meet growing demand, and advance development of new materials and capabilities. Schooner Capital, a prominent Boston-based private investment firm, led the round, joined by key existing investors such as Fine Structure Ventures, Foundation Capital, Corazon Capital, 11.2 Capital, and Build Collective.
“Mantle is poised to revolutionize the global tooling industry,” stated Alexandra Manick, Principal at Schooner Capital. “Their TrueShape manufacturing platform has demonstrated substantial cost savings and unprecedented speed for customers. This transformative solution addresses critical challenges in skilled labor shortages and accelerates product development timelines for industrial toolmakers and OEMs worldwide.”
Reshoring Manufacturing with 3D Printing: Enhancing Independence and Efficiency
The recent trend towards reshoring manufacturing to the United States underscores the pressing need for innovative solutions that reduce costs and enhance production efficiencies amidst global supply chain vulnerabilities. Metal 3D printing has emerged as a pivotal technology reshaping American manufacturing’s future.
“The current fragility of global supply chains has spurred a significant reshoring effort, dramatically increasing demand for molded parts and, consequently, toolmaking,” noted Ted Sorom, CEO and co-founder of Mantle. “We’re navigating dual challenges: a shrinking U.S. toolmaking workforce and escalating costs and lead times due to constrained capacities. Manufacturers are increasingly turning to groundbreaking solutions. For our forward-thinking clients, adopting Mantle’s tooling technology has become pivotal in boosting labor productivity, cutting expenses, and vastly reducing lead times.”
Addressing Toolmaker Labor Shortages
Amidst acute shortages of toolmakers and skilled tradespeople in manufacturing—driven by an aging workforce and surging demand for essential tooling—automation and advanced technologies are becoming crucial.
Heyco Products, a U.S.-based manufacturer of wire protection products and electrical components, integrated Mantle technology into its molding and toolmaking operations.
“We chose Mantle to accelerate product launches and enhance our toolroom efficiency while attracting young talent to Heyco,” said Danny Anthony, Vice President of Operations at Heyco. “By employing Mantle for mold tooling, we’ve accelerated one product’s time-to-market by two months compared to conventional methods. Our toolmakers now have access to cutting-edge technology that significantly boosts their productivity.”
General Pattern, a fourth-generation, woman-owned manufacturer specializing in plastic forming, adopted Mantle’s advanced 3D printing to streamline tool production, slashing lead times and labor costs.
“Mantle’s metal 3D printing technology isn’t just innovation—it’s a leap towards securing our legacy,” remarked Denny Reiland, CEO of General Pattern.
Positioned for Accelerated Tooling Growth
With substantial growth in shipments over the past year, Mantle’s precision metal 3D printing technology is tailored for printing injection mold tools, a niche where traditional methods often fall short. This innovation reduces both time and costs associated with high-quality mold and die fabrication, offering unparalleled precision, surface finish, and metal properties while automating production and reducing reliance on scarce skilled labor.
Mantle’s technology has been integral in producing millions of end-use parts across diverse sectors, from medical devices to industrial components. By focusing on tooling rather than end-part production, the company has slashed costs for customers by over 65% and accelerated development cycles by up to 90%, cementing its role as a leader in advancing manufacturing efficiency and sustainability.