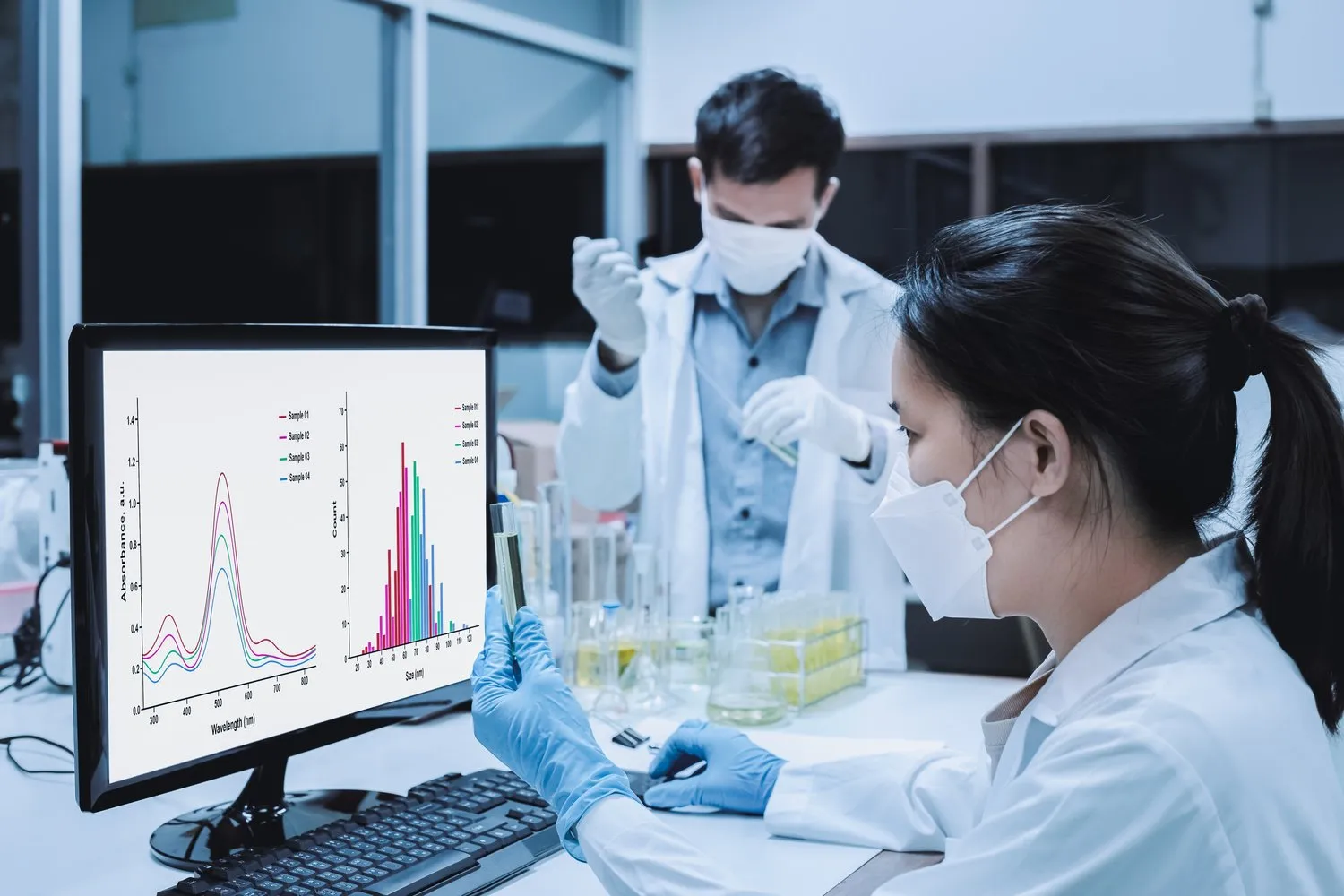
Shin-Etsu Chemical and Hokkaido University Launch Advanced Lipid Nanoparticle Production System for Scalable and Flexible Pharmaceutical Manufacturing
Shin-Etsu Chemical headquartered in Tokyo and led by President Yasuhiko Saitoh, in partnership with Hokkaido University, located in Hokkaido under the leadership of President Kiyohiro Houkin, has announced the development of a cutting-edge production system for lipid nanoparticles (LNPs). This newly designed system incorporates a sophisticated microfluidic device as a central component and represents a breakthrough in both the precision and scalability of LNP manufacturing.
Production of this innovative system is scheduled to begin in April 2025, with Lilac Pharma Inc., a Hokkaido-based pharmaceutical firm helmed by President Motoki Susa, designated as the official distributor. This collaboration marks a significant milestone in pharmaceutical engineering, combining academic innovation with industrial application to address pressing global health needs.
The Rising Role of Lipid Nanoparticles in Modern Medicine
Lipid nanoparticles have gained widespread attention in recent years due to their pivotal role in the successful deployment of mRNA vaccines during the COVID-19 pandemic. These nano-sized particles, primarily composed of lipids, are used to encapsulate and deliver nucleic acids such as mRNA into cells, where they can then produce proteins to trigger an immune response or correct genetic dysfunctions. The ability of LNPs to protect fragile nucleic acid molecules and facilitate their uptake by human cells has made them indispensable in both vaccine development and the advancement of genetic medicine.
Beyond COVID-19 vaccines, LNPs are poised for broader application in the prevention and treatment of various infectious diseases and types of cancer. Their utility in the delivery of personalized therapies, including RNA-based and gene-editing treatments, places them at the heart of next-generation pharmaceutical innovation. However, one of the significant challenges in the widespread adoption of LNP-based therapies has been the difficulty in scaling up production while maintaining precise control over particle size and quality.
Microfluidic Devices: A Technological Leap in LNP Production
In traditional LNP manufacturing methods, bulk mixing techniques often lead to variability in particle size and composition. This inconsistency can compromise drug efficacy and safety. To address this, researchers and manufacturers have increasingly turned to microfluidic technology.
Microfluidic devices, featuring microscopic channels that range from a few micrometers to several hundred micrometers in width, allow for the controlled mixing of lipid and nucleic acid solutions at a microscale. By leveraging the principles of fluid dynamics, these devices enable highly reproducible and tunable LNP production. The result is improved particle uniformity and greater control over key attributes such as size, distribution, and encapsulation efficiency.
However, despite these advantages, early microfluidic systems were limited in their practical application due to low throughput. Existing devices were largely suited for research and small-batch production, lacking the capacity needed for large-scale pharmaceutical manufacturing.
A Breakthrough in Scalable Microfluidic Design
The new system developed by Shin-Etsu Chemical and Hokkaido University addresses this bottleneck by combining state-of-the-art material science and device engineering. At the heart of the system is Hokkaido University’s proprietary iLiNP® microfluidic device—a platform that has undergone extensive optimization for enhanced performance and reliability.
This device is fabricated using synthetic quartz, a specialty material provided and processed by Shin-Etsu Chemical. Synthetic quartz offers exceptional durability, chemical resistance, and optical clarity, making it ideal for microfluidic applications where precision and sterility are paramount. The company’s advanced materials and processing technologies ensure that the microfluidic channels are finely tuned to deliver consistent flow dynamics and mixing efficiency.
To facilitate industrial-scale application, Shin-Etsu Chemical collaborated with its subsidiary, Shin-Etsu Engineering, which contributed system integration expertise and ensured the new LNP production platform meets the rigorous standards of Good Manufacturing Practice (GMP). GMP compliance is essential for pharmaceutical equipment, as it guarantees that products are manufactured under strict protocols that ensure quality, safety, and efficacy.
Versatile System Design for Diverse Pharmaceutical Needs
One of the most notable features of this newly developed LNP production system is its versatility. The system is designed to be highly modular and space-efficient. Occupying just one square meter, it can be installed in a variety of settings—from research labs and hospital manufacturing units to large-scale production facilities.
The system’s design enables seamless adjustment of production volumes based on demand. Whether the need is for small-batch, high-mix production of experimental nanomedicines or the mass production of standardized vaccines, the same system can adapt accordingly. This flexibility is critical in a world where pharmaceutical needs can shift rapidly, especially in the face of emerging infectious diseases or pandemics.
Moreover, the system supports the production of diverse LNP formulations. This is particularly beneficial for personalized medicine, where treatments must be tailored to the genetic and physiological profiles of individual patients. By enabling small-batch production with high precision, the platform facilitates the creation of bespoke therapies while retaining the capacity to pivot to high-throughput production as needed.
A Vision for Pandemic Readiness and Future-Proof Infrastructure
In the wake of the COVID-19 pandemic, the importance of rapid-response manufacturing infrastructure has become increasingly clear. Shin-Etsu Chemical and Hokkaido University envision their LNP production system as a core component of a more resilient pharmaceutical supply chain.
By deploying this system as a flexible manufacturing platform, institutions and companies can maintain readiness for both everyday therapeutic production and emergency vaccine manufacturing. During periods of relative normalcy, the system can be used to support research, pilot studies, and commercial production of nanomedicines. In times of crisis, the system can pivot to produce large volumes of critical vaccines with minimal reconfiguration.
This dual-use capability could revolutionize pharmaceutical logistics and planning, offering governments, biotech firms, and healthcare providers a reliable and scalable solution for future health emergencies.
Upcoming Innovations: Benchtop System for Research and Development
In addition to the mass-production system, the joint research team from Shin-Etsu Chemical and Hokkaido University is actively developing a benchtop version of the LNP production platform. This smaller, more compact device is intended for use in laboratory and R&D environments, where flexibility, ease of use, and low-volume production are critical.
The prototype for the benchtop unit is expected to be completed by the end of 2025. This device will support early-stage research by allowing scientists to quickly test new LNP formulations and delivery strategies without the need for full-scale equipment. The goal is to create a seamless pipeline from initial research to commercial manufacturing, supported by a family of compatible production systems.
By offering a suite of tools that cater to different phases of drug development—research, clinical trials, and mass production—Shin-Etsu Chemical and its partners are building a robust ecosystem for the future of nanomedicine.
A Commitment to Innovation and Societal Contribution
Shin-Etsu Chemical’s involvement in this project reflects its broader corporate philosophy: using scientific and technological expertise to contribute to a sustainable and prosperous society. The company has long been a leader in materials science and advanced manufacturing technologies. With this latest innovation, it reaffirms its commitment to solving global challenges through collaboration, innovation, and responsible business practices.
Meanwhile, Hokkaido University’s role in the development process underscores the importance of academic-industry partnerships. The university has a strong track record in nanotechnology and bioengineering research, and its iLiNP® technology represents a culmination of years of work in microfluidic systems for drug delivery.
Together, these institutions exemplify how cooperative innovation can lead to transformative solutions with wide-reaching impact.
Glossary
Microfluidic Devices
Specialized tools that contain channels with microscopic dimensions, typically ranging from a few to several hundred micrometers in width. These devices enable the controlled handling of minute fluid volumes, making them ideal for applications in chemical analysis, biological studies, and nanomedicine production.
Lipid Nanoparticles (LNPs)
Nano-scale structures composed mainly of lipids that encapsulate nucleic acids or other active ingredients. LNPs are widely used in modern drug delivery systems, particularly in mRNA vaccine platforms.
GMP (Good Manufacturing Practice)
A system of guidelines that ensures products are consistently produced and controlled according to quality standards. GMP regulations are enforced to protect consumers from ineffective or unsafe pharmaceutical products.
Personalized Medicine
A healthcare approach that tailors medical treatments to individual patient characteristics, including genetic makeup, lifestyle, and environment. Personalized medicine aims to optimize therapeutic efficacy and minimize side effects.